Epilog Fusion Pro Lasers - 24, 36 and 48
Introducing the new Epilog Fusion Pro. 5G acceleration and 165 IPS engraving speeds provide the fastest laser engraving in the industry. Whether you’re engraving wood, plastic, coated metals or glass, the Epilog Fusion Pro laser allows you to process more product in less time. Placing your artwork is easier than ever too, with the new IRIS™ Camera Positioning feature. Overhead cameras enable you to view your material as it is arranged on the table, allowing you to accurately place your artwork and know exactly where your laser will engrave.
Fusion Pro 24: 24” x 24” (610 x 610 mm)
Fusion Pro 36: 36” x 24” (914 x 610 mm)
Fusion Pro 48: 48” x 36” (1220 mm x 914 mm)
Wattages available:
- CO2: 50, 60, 80, or 120 watts
- Fiber: 30 or 50 watts
- Dual: Configure your laser with both CO2 and Fiber sources
Specifications and Compatible Materials
Epilog Fusion Pro Specifications
Compatible Materials - CO2 Lasers
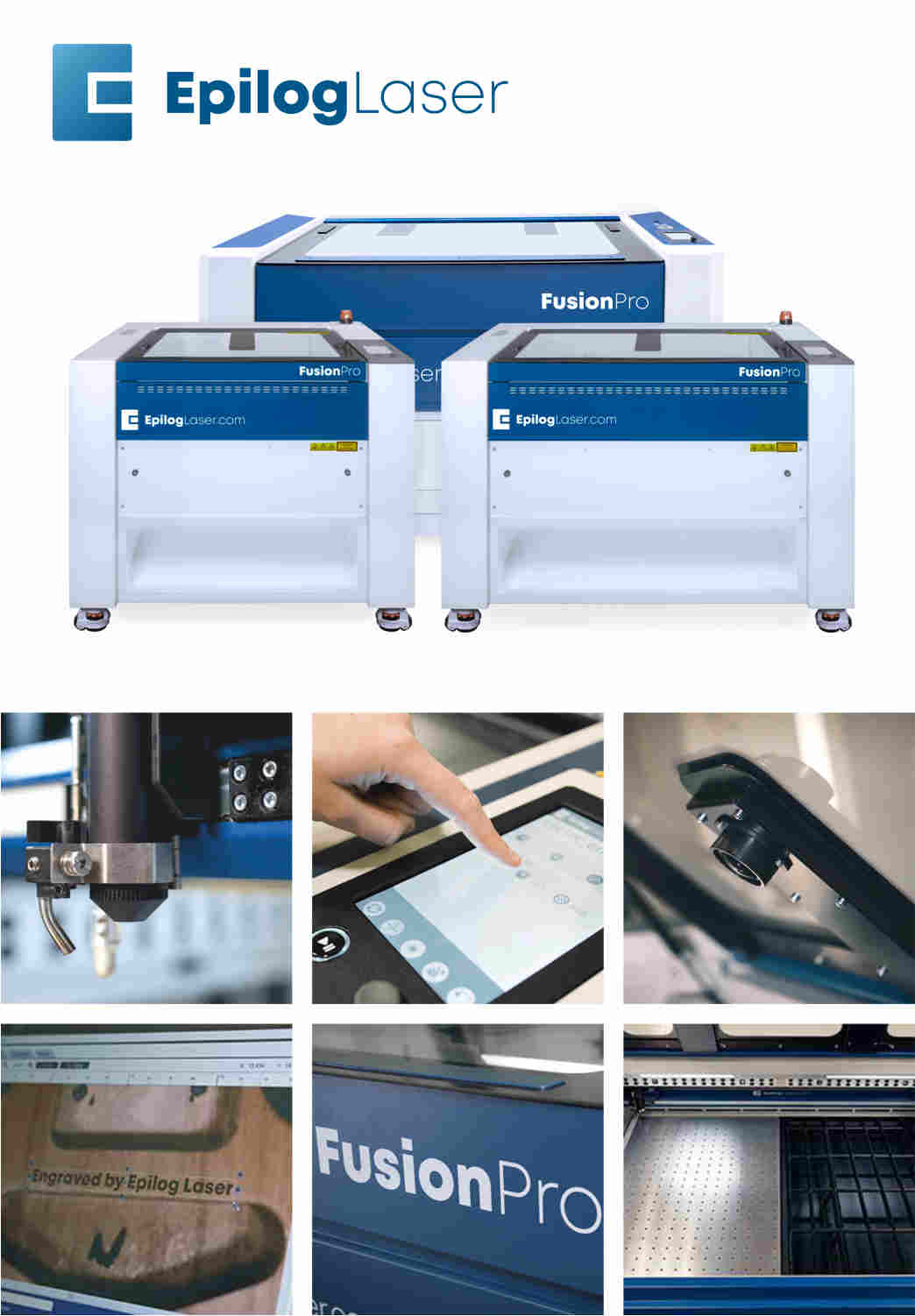
FUSION PRO TOUR
Explore the Epilog Fusion Pro Laser series in our video for a comprehensive tour of its cutting-edge features. Uncover its unmatched design and performance, whether you're a seasoned professional or new to laser technology.
Fusion Pro LASER SERIES FEATURES
Check out some of the most impressive features of the Fusion Pro laser series below.
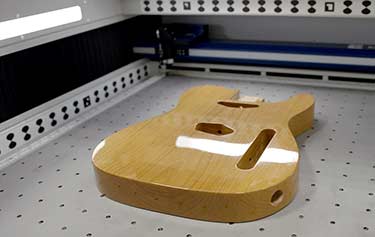
Highest-Speed Engraving Over Largest Work Area
The Fusion Pro’s 165 IPS engraving speed and 5G acceleration combine to provide the fastest engraving in the industry.
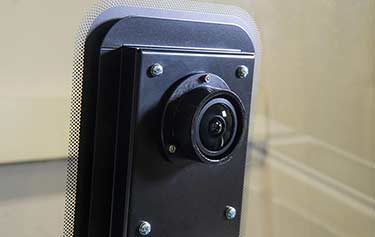
IRIS™ Camera Positioning
Overhead cameras provide an accurate picture of the working area for precise artwork placement. Drag and drop your artwork on screen for the fastest work processing.
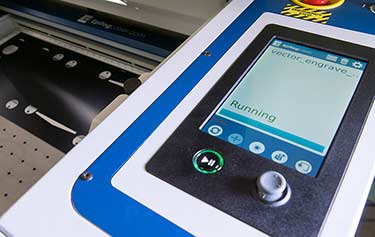
Touch Screen at the Laser
Select between jobs, auto focus the laser, and rerun jobs at the touch of a button from the easy-to-use touch screen interface right at the laser.
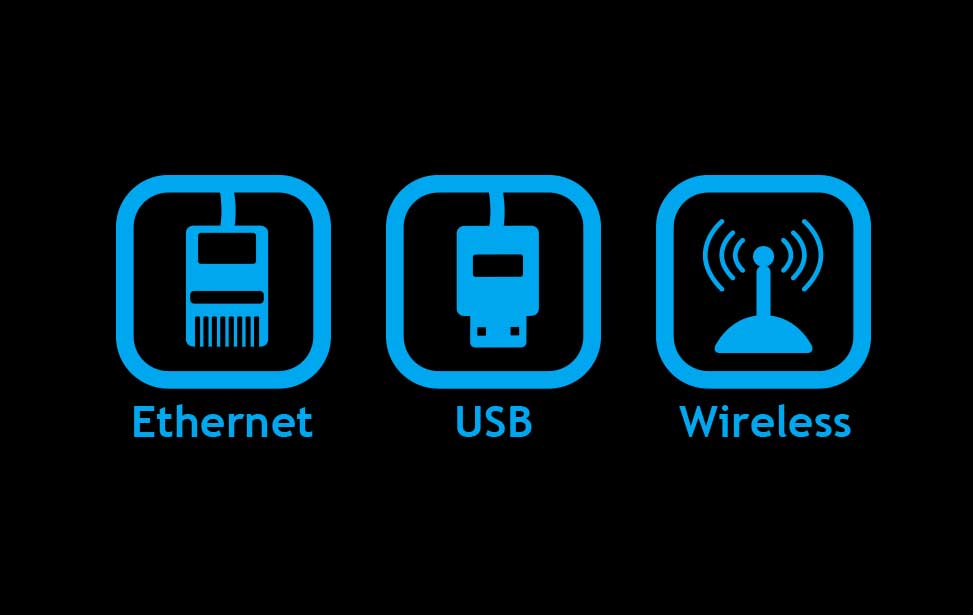
Network Your Laser Across Your Business
The Fusion Pro features built-in Ethernet, USB, and coming soon, a new wireless connection for more options for networking your laser.
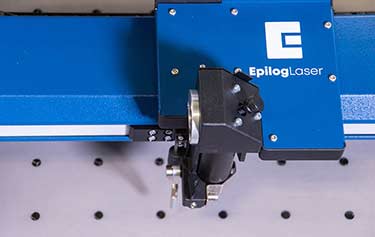
SAFEGUARD™ Features
Keep the mechanics of your laser machine cleaner than ever before with side bellow enclosures, a fully covered x-axis assembly, and covered lens assembly.
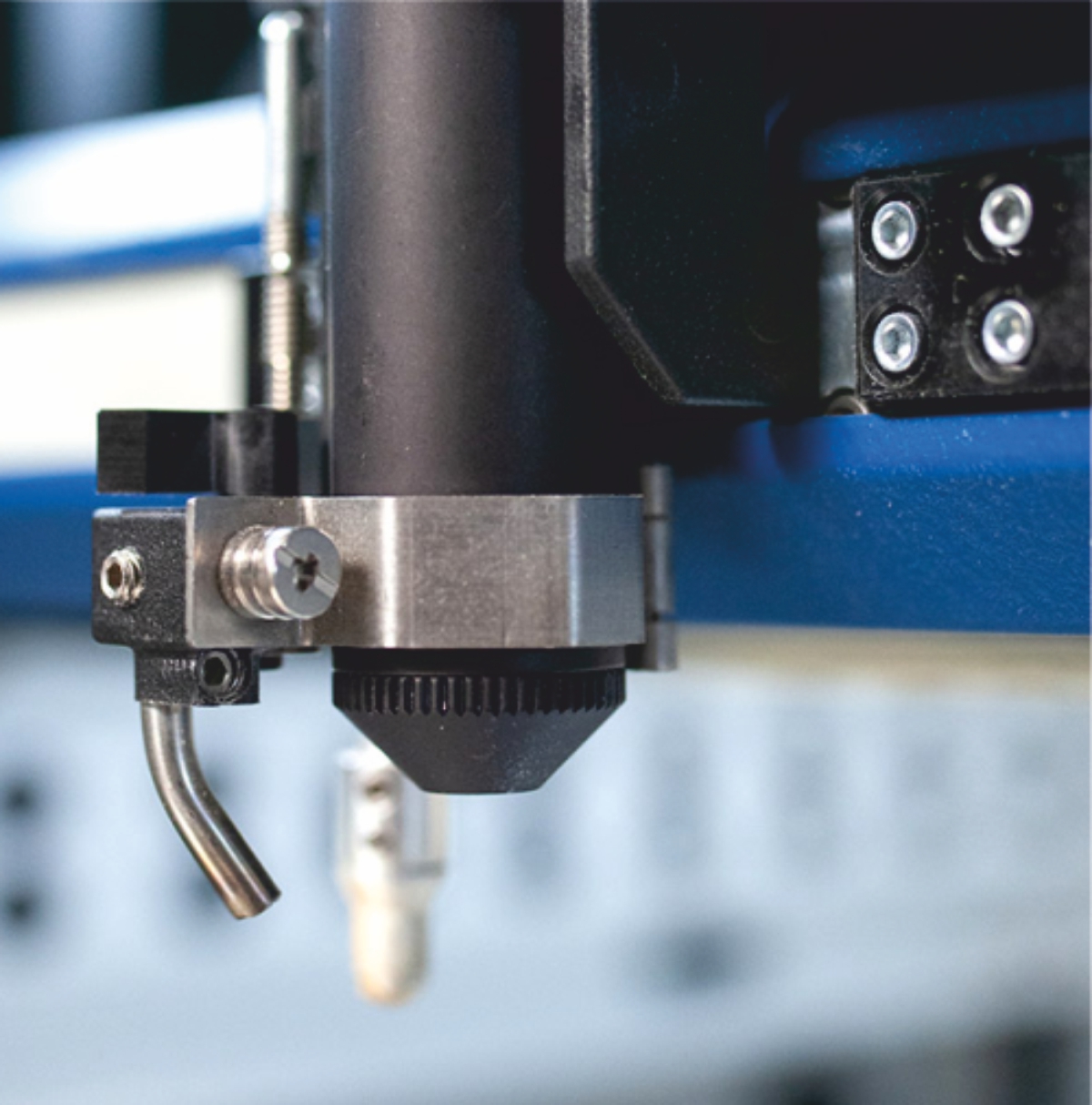
Air Assist and Compressor
The air assist removes heat and combustible gases from the cutting surface for a cleaner cut. A built-in air compressor provides air directly to the work surface.
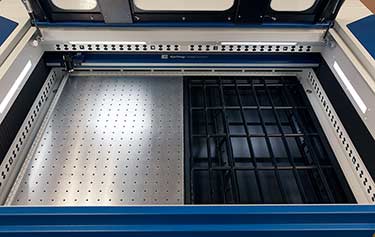
Table Choices
Mix and match your table across the bed with optional slat and gridded cutting tables.
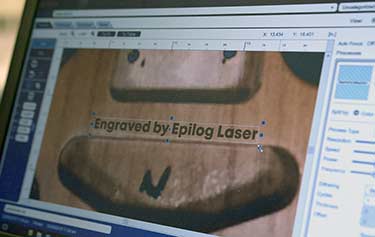
1 GB Memory in the Machine
Improve job management and data integrity with 1GB of RAM in both Fusion Pro systems. Save your most run jobs right at the laser.
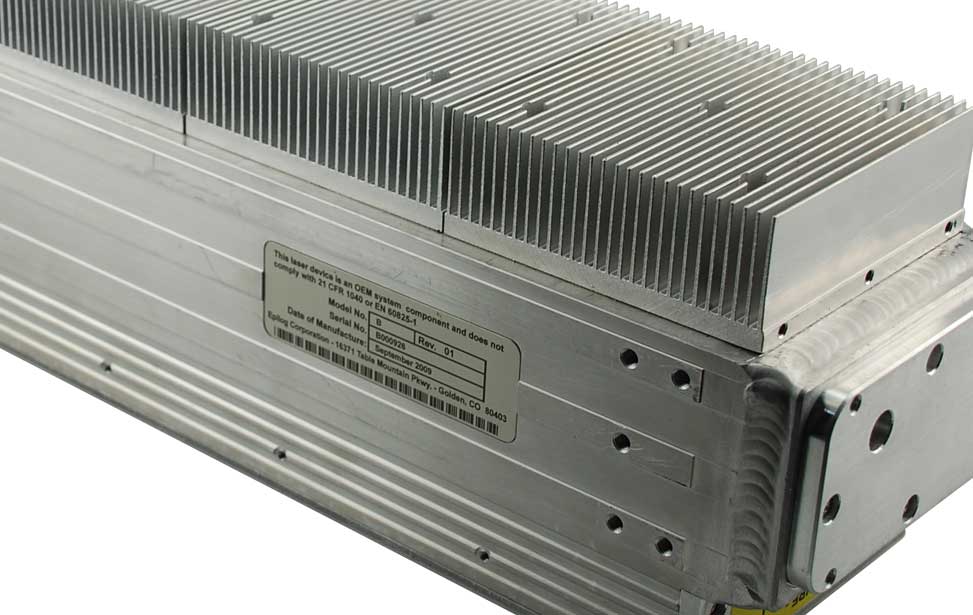
CO2 Waveguide Laser Tube by Epilog
All-metal tube design provides higher beam quality and longer life with low recharge costs.
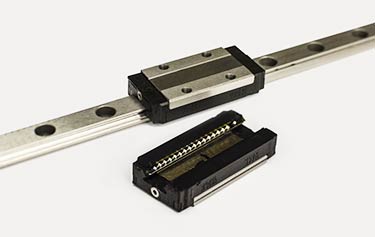
Long-Life Steel Bearing
A dual block design provides the most rigidity and reduced vibration eliminating the inevitable wobble and replacement of plastic bearings